The ceiling plays an important role in both the structural integrity and aesthetics of a space. Periodic inspections are necessary to identify cracks, water stains, and other issues that require repair. Contact Ceiling Repairs Perth for professional help.
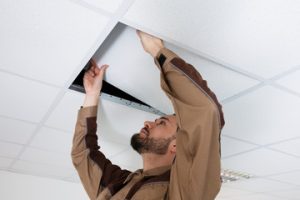
Small holes can often be patched with plaster compound; however, widespread damage may call for a full replacement. Proper priming and painting help achieve a polished restoration look.
Drywall is a popular choice for residential walls and ceilings. It is sturdy, easy to install, and provides a great base for painting and other decorative treatments. But like any construction material, drywall is vulnerable to damage and wear. Cracks, holes, dents, and discoloration are common problems that often need repair. Small blemishes and isolated cracks are easy enough to fix, but larger dings and dents will require more extensive work to properly repair.
Fortunately, there are many ways to repair minor drywall damage. A simple visual inspection is a good way to catch minor issues before they worsen. Proactively addressing these minor problems will minimize future damage and prevent expensive repairs.
When it comes to large dents or holes, you can patch them with spackle or joint compound. Simply clean out the damaged area and apply a light coating of compound to the surface. Smooth the compound with a putty knife and feather the edges to ensure that the repaired surface blends seamlessly with the surrounding wall. Once the compound dries, you can sand and prime it to match the existing wall color.
More extensive cracks are another common problem that needs to be addressed quickly. If you see a crack that is wider than 1/8 inch, or if it appears on a sagging or uneven wall, this indicates a serious structural issue and should be fixed by a professional. Cracks that are caused by humidity, or that appear along with moisture damage, also require professional attention.
A professional can help you select the right drywall materials for your home and can provide installation services. They can also recommend energy efficient insulation and low-VOC paints that will improve indoor air quality. They can even install drywall with mold-resistant additives to protect against dampness and decay.
In addition to repairing drywall, an experienced contractor can help you update your home’s decor with new paint and trim. They can also add crown molding, if needed, to enhance your ceiling’s appearance. They can also upgrade your drywall to green board, which contains additives that prevent the growth of mold and mildew.
Plaster Repair
Plaster walls are often beautiful and add to a home’s historical value, but they can also be fragile. Regular inspections are the key to preventing extensive damage, and catching problems early so they can be repaired. Often, simple repairs are enough to address minor cracks and holes, but extensive damage, large bulges, or signs of structural issues may require professional help.
Inspect your plaster walls for signs of wear and tear, including hairline cracks and holes. While these are common, it is important to note any areas where the plaster seems springy or disconnected from the lath. These spots should be stabilized and may need to be replastered.
To repair plaster cracks, first clear away any loose bits and sand the area smooth with a wallboard knife. Then, apply a thin layer of joint compound to the cracks and feather the coverage out about 3″ around each crack to help it blend with the rest of the wall. After the second coat dries, sand again with a fine-grit sandpaper to create a smooth finish.
Depending on the extent of the damage, you will need to replaster these areas. When you do, make sure to use a non-sag filler designed for ceilings. Also, follow the manufacturer’s instructions to mix the plaster and pour it into a mud pan or bucket. Then, use a plastering trowel to spread the filler in even layers. Make sure to start on the left side of the damaged area and move towards the right to ensure an even finish.
When replastering, it is important to remember that plaster doesn’t harden by air drying and will actually set faster when you physically mix it with a tool. This is because it heats up due to the exothermic reaction that occurs when the plaster mixes with water.
When repairing cracks or holes in plaster walls, be sure to wear a mask and goggles to protect yourself from the dust. After you’re finished sanding, apply a coat of primer designed for plaster to protect your work and make the repaired area ready to paint.
Soffit Repair
Although soffits are not usually a focal point in your home, they are vital for attic ventilation and should be maintained regularly to prevent water damage. Neglecting soffit damage can lead to a number of issues, including moisture buildup and mold growth. This can lead to health and structural problems for occupants. Regular soffit maintenance can help prevent the need for extensive repairs.
The cost of soffit repair depends on the extent of the damage and the materials needed. Labor costs are also a factor, as are other expenses such as scaffolding and equipment rental, disposal of old materials, and permit fees if required. In general, minor repairs such as patching holes or sealing cracks will cost less than extensive repair jobs that involve replacing large sections of the soffit or addressing underlying issues.
Before attempting a soffit repair, be sure to wear proper safety gear and work from a stable ladder or platform. Thoroughly inspect the soffit for damage, especially areas of rot or water damage. If the soffit is infested with mold or mildew, treat it with a mold and mildew remover. If necessary, remove shingle molding from the fascia boards to access the soffit. If the soffit is nailed to the fascia, use a pry bar to remove nails or screws without damaging the surrounding areas of the roof. Once the damaged soffit has been removed, measure the dimensions of the area and cut replacement soffit panels to size using a circular saw or jigsaw. If the soffit is not completely rotten, you can nail the replacement panel in place with galvanized nails or screws.
Once the new soffit is installed, seal the joints with caulk to prevent moisture infiltration. If necessary, paint the replacement soffit to match the color of the existing trim.
To keep the soffit looking its best, you should regularly clean it with a brush or hose and a mild detergent. Be sure to check for moss or mildew growth as well as bee, hornet, or wasp nests. These can create a barrier to attic ventilation and should be removed promptly.
Acoustical Ceiling Repair
Acoustic ceiling tiles help control sound, but they can get damaged and need to be fixed. It’s easy to ignore small blemishes and cracks, but these issues can cause bigger problems and affect how well the tile works. Knowing how to spot water damage and a pro’s help for hidden problems keep these tiles last longer, work better, and look great.
If a ceiling tile is stained or discolored, a simple repair with RENEW can restore it to its original condition. This coating is specially formulated for acoustical ceiling tiles and stucco. Unlike traditional paint, which can compromise the fire safety and acoustical performance by clogging their pores, RENEW maintains these important properties. It is nonflammable when dry and free of chlorinated solvents, making it an environmentally responsible choice.
Staple lifter: The simplest way to remove damaged tiles from the ceiling grid is with an Arrow SL24D staple lifter. This tool can easily remove the acoustical ceiling tile staples without damaging the grid. After the staples are removed, replace the damaged ceiling tile and re-staple it to the framework with the proper amount of pressure. Then use the appropriate drywall screws for your ceiling.
Water damage: If acoustic ceiling tiles are warped, sagging, or discolored, the problem might be water damage. Moisture can rot the tile and damage its insulation. Check for mold, mildew and other signs of moisture on the ceiling. If any are found, a professional must assess the extent of the water damage to determine how serious it is and if the structure of the ceiling needs to be reinforced.
A professionally assessed and repaired acoustic ceiling will last longer, work better and look good. It’s also the best way to prevent health risks from bad air quality, which can result from a ceiling that’s not working correctly. The good news is that acoustic ceilings are usually easy to fix, so it’s worth checking them regularly. Repairing minor blemishes and fixing water damage early on makes your acoustic ceiling last longer, looks better, and helps control sound and temperature.